Flexible, lightweight, versatile
Non-solvent Lamination
Non-solvent lamination adhesive is a type of adhesive that is used to bond two or more layers of material together without the use of a solvent. Solvents are typically used in adhesives to dissolve the adhesive and allow it to spread evenly over the surface of the materials being bonded. However, solvent-based adhesives can have negative environmental and health impacts, so non-solvent alternatives have been developed as a more sustainable option. These types of adhesives are typically applied using a roller or a brush, and can be made from a variety of materials such as acrylics, polyurethanes, and natural rubber. Non-solvent adhesives also have advantages such as faster drying time and low VOC emissions, which help to keep the air clean.
Lamination Types
Dry Lamination
In the process of dry lamination, bonding agents are applied to substrates that have been dissolved into a liquid form. The substrate is then dried in an oven to remove any remaining bonding material. After this step, an adhesive is applied to the substrate and it is then laminated to another substrate through the use of high pressure and heated rollers. This approach improves the strength of the laminate.
Wet Lamination
In the process of dry lamination, bonding agents are applied to substrates that have been dissolved into a liquid form. The substrate is then dried in an oven to remove any remaining bonding material. After this step, an adhesive is applied to the substrate and it is then laminated to another substrate through the use of high pressure and heated rollers. This method improves the strength of the laminate.
Soventless Lamination
Solvents are not used in the production of adhesive substances when using solventless adhesives. This method requires two or more substrates that react during the lamination process, eliminating the need for any drying component. The result of this process is a laminated web that is rewound into a complete roll.
Wax Lamination
In this method, the bonding agent is in a heated, melted state and is applied to a single substrate.
In the process of dry lamination, bonding agents are applied to substrates that have been dissolved into a liquid form. The substrate is then dried in an oven to remove any remaining bonding material. After this step, an adhesive is applied to the substrate and it is then laminated to another substrate through the use of high pressure and heated rollers. This approach improves the strength of the laminate.
In the process of dry lamination, bonding agents are applied to substrates that have been dissolved into a liquid form. The substrate is then dried in an oven to remove any remaining bonding material. After this step, an adhesive is applied to the substrate and it is then laminated to another substrate through the use of high pressure and heated rollers. This method improves the strength of the laminate.
Solvents are not used in the production of adhesive substances when using solventless adhesives. This method requires two or more substrates that react during the lamination process, eliminating the need for any drying component. The result of this process is a laminated web that is rewound into a complete roll.
In this method, the bonding agent is in a heated, melted state and is applied to a single substrate.
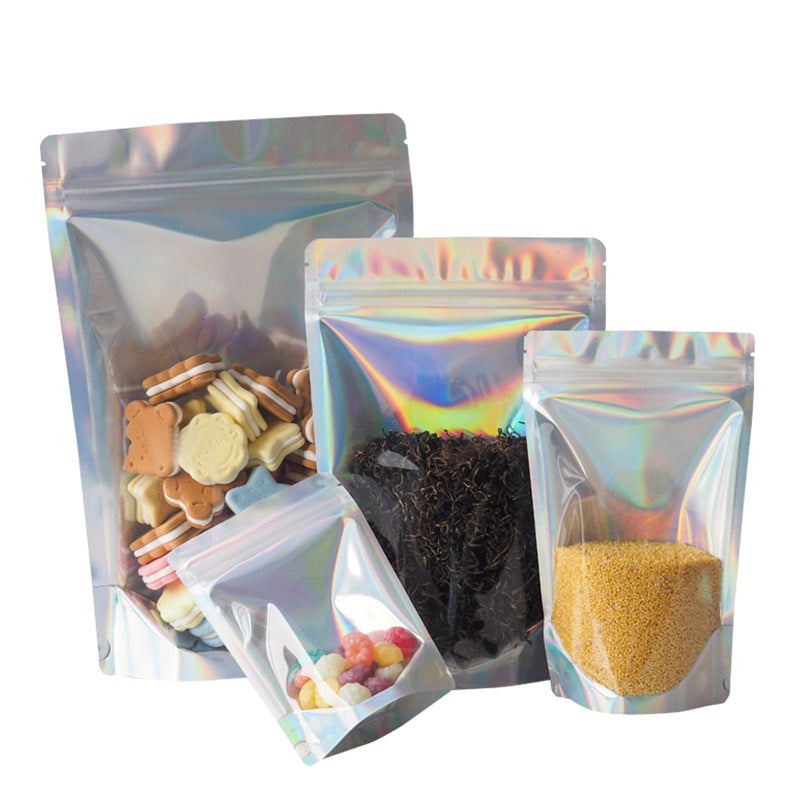
Applications for Non-solvent Lamination
- Lamination of food packaging materials, such as pouches and bags, to create a barrier against moisture, oxygen, and other contaminants that can affect the shelf life of the food.
- Lamination of medical and pharmaceutical packaging materials, such as blister packs and sachets, to create a barrier against moisture and other contaminants that can affect the potency and effectiveness of the medication.
- Lamination of industrial packaging materials, such as bags and covers, to create a barrier against moisture, dust, and other contaminants that can affect the performance of the packaged goods.
- Lamination of decorative packaging materials, such as labels and boxes, to create a glossy finish or to add a design or pattern to the packaging.
Comparing
Solvent Based with Water based
1. Strong bond: Solvent-based adhesives create a strong bond between the two surfaces being laminated, which helps to ensure that the finished product is durable and long-lasting.
2. Fast drying time: Solvent-based adhesives dry quickly, which allows for faster production times and helps to minimize downtime.
3. Good for high-temperature applications: Solvent-based adhesives can withstand high temperatures, making them well-suited for laminating products that will be exposed to heat.
4. Can be used with a wide range of materials: Solvent-based adhesives can be used with a variety of materials, including plastics, metals, and composites, which makes them a versatile option for lamination.
5. Cost-effective: Solvent-based adhesives are typically less expensive than other types of adhesives, which can help to keep production costs low.
1. Environmental Sustainability: Solvent-based lamination uses chemicals that can posibly be environmental unfriendly. Non-solvent based methods are considered to be more eco-friendly.
2. Safety: Solvents used in lamination can be flammable, toxic and can cause health problems if inhaled. Non-solvent based methods are considered safer to use.
3. Cost: Non-solvent based lamination methods can be less expensive than solvent-based methods, as they do not require the use of expensive chemicals.
4. Performance: Non-solvent based lamination methods
can provide better performance in terms of strength and durability, making it ideal for certain types of applications especially in packaging and automotive industry.
5. Flexibility: Non-solvent based lamination can provide more flexibility in terms of the types of materials that can be laminated and the thicknesses that can be achieved.
1. Health and safety concerns: Solvents used in this process can be toxic and flammable, and can cause respiratory and skin irritation. This can be a concern for workers who are exposed to these chemicals on a regular basis.
2. Environmental impact: Solvent-based lamination can release volatile organic compounds (VOCs) into the air, which can contribute to air pollution and harm the environment.
3. Long drying times: Solvent-based lamination requires drying time for the solvent to evaporate, which can slow down the production process.
4. Quality concerns: Solvent-based lamination can cause wrinkling or bubbling in the laminated material, which can affect the final quality of the product.
1. Limited adhesion: Non-solvent based lamination may not provide as strong of an adhesive bond as solvent-based methods.
2. Increased curing time: The curing process for non-solvent based lamination can take longer than solvent-based methods.
3. Higher cost: Non-solvent based lamination may be more expensive than solvent-based methods due to the materials and equipment required.
4. Limited materials compatibility: Non-solvent based lamination may not be compatible with all types of materials, limiting its use in certain applications.
5. Reduced flexibility: Non-solvent based lamination
may result in a less flexible finished product compared to
solvent-based methods.
Let's Connect