Extrusion and Adhesive Lamination
Built with a focus on providing top-quality performance and reliability.
Our advanced extrusion and adhesive lamination technology will fine-tune your packaging requirements. We offer exceptional extrusion development services, including extrusion capabilities and expert guidance, enhance current product lines and explore new material options for barrier rigid food packaging, thermoforming rollstock, and heat seal seal rollstock. Our goal is to provide top-quality support to help you succeed in the industry.
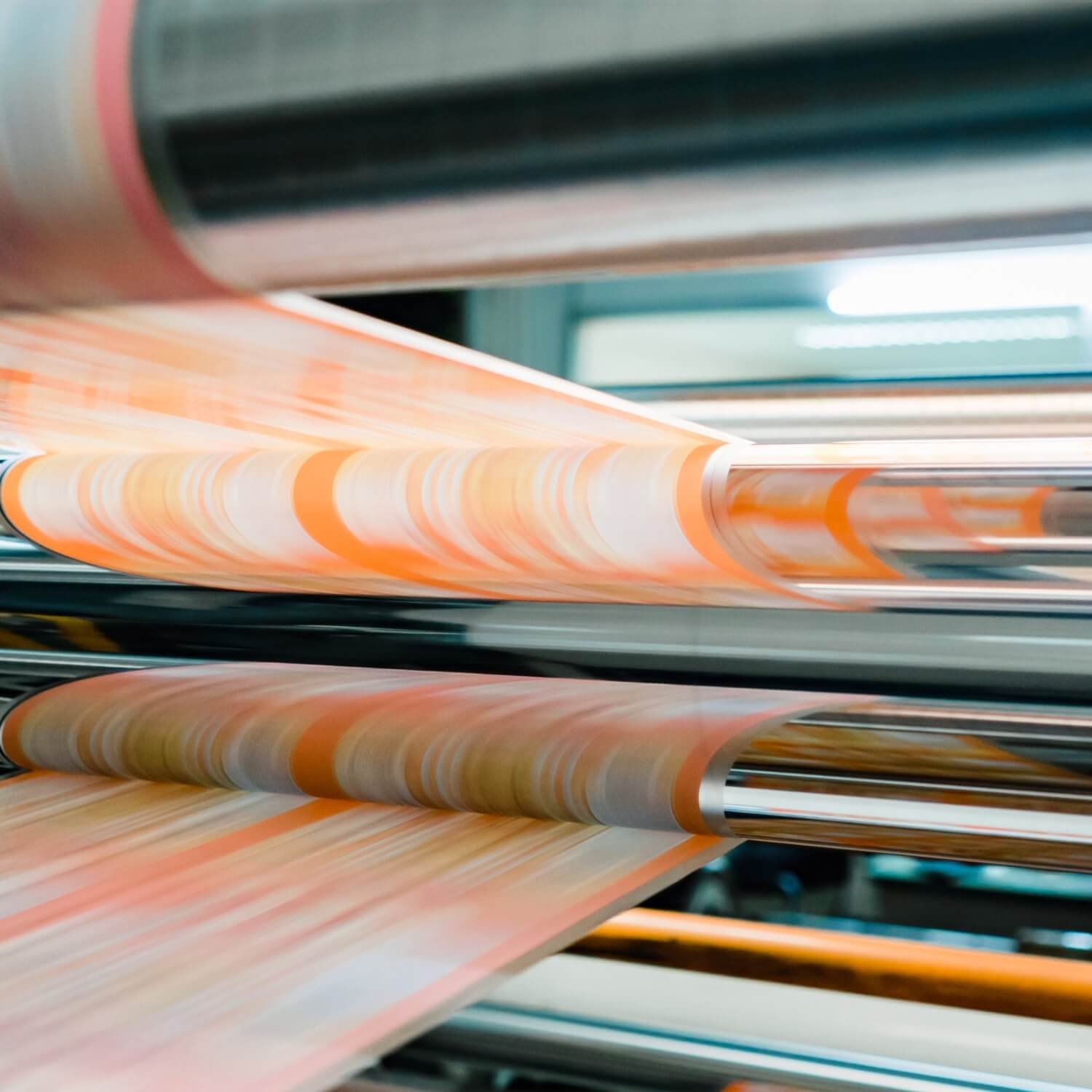
Adhesive and Extrusion Lamination Process
In adhesive lamination, a film material is bonded to another film using an adhesive. This process can be repeated with multiple layers to create a multi-layered film structure, or it can be combined with extrusion lamination to create a flexible packaging material with both adhesive and extrusion properties. In the extrusion lamination process, two films are brought together extruded through computer-controlled dies with advanced gauge controls, such as automatic gauge monitoring profile control. This creates a multilayer flexible packaging lamination. The process can be repeated to create the final flexible packaging structure, or it can be combined with adhesive lamination to complete the flexible packaging.
Explore Extrusion LaminationExplore the possibilities
1. Monolayer extrusion
Thin, single-layered rollstock made from a carefully chosen substrate material can be customized to specific size and shape requirements. The selection of performance resins and additives is also an option to ensure optimal performance.
2. Extrusion Lamination
Customize your barriers to meet your specific needs:
Custom barrier specifications: You can specify the dimensions, shape, and other characteristics of your barriers to suit your specific needs.
Custom substrate selection: You can choose from a range of substrate materials, including plastic, metal, and glass, to create a barrier that is durable and suitable for your application.
Easy-peel and weld-seal: These features allow you to easily install and remove the barriers, making them convenient for use in a variety of settings.
Performance resins and additive selection: You can choose from a range of performance resins and additives to optimize the strength, durability, and other properties of your barriers.
3. Multi-layer Coextrusion
Custom barriers can be created to meet specific requirements. These barriers can be configured by mutli-layer films in order to meet the optmial barrier performance. The selection of performance resins and additives can also impact the effectiveness of the barriers as an additonal option.
Thin, single-layered rollstock made from a carefully chosen substrate material can be customized to specific size and shape requirements. The selection of performance resins and additives is also an option to ensure optimal performance.
Customize your barriers to meet your specific needs:
Custom barrier specifications: You can specify the dimensions, shape, and other characteristics of your barriers to suit your specific needs.
Custom substrate selection: You can choose from a range of substrate materials, including plastic, metal, and glass, to create a barrier that is durable and suitable for your application.
Easy-peel and weld-seal: These features allow you to easily install and remove the barriers, making them convenient for use in a variety of settings.
Performance resins and additive selection: You can choose from a range of performance resins and additives to optimize the strength, durability, and other properties of your barriers.
Custom barriers can be created to meet specific requirements. These barriers can be configured by mutli-layer films in order to meet the optmial barrier performance. The selection of performance resins and additives can also impact the effectiveness of the barriers as an additonal option.
Value added extrusion lamination in manufacturing processes.
Extrusion lamination has a distinct advantage when it comes to thickness, stiffness, or puncture resistance, thanks to the added bulk provided by the molten resin. For example, we can use extrusion lamination to combine two 70-gauge films with seven pounds of polyethylene, resulting in a 180-gauge lamination. This is a more cost-effective way to increase thickness compared to purchasing higher gauge film. Additionally, the thickness of the resin layer can be customized to meet specific needs. While adhesive lamination is more common, fewer converters have extrusion lamination lines due to the higher initial equipment cost. However, the benefits of extrusion lamination, such as cost-effective rigidity or thickness, enhanced barrier properties, and increased puncture resistance, make it a valuable investment for packaging film production.
One way to cost-effectively add rigidity or thickness to a material is by using reinforcing materials, which can be incorporated into the base material to improve its mechanical properties.
Most commonly, barrier properties refer to a material's ability to block the passage of gases, liquids, or other substances. Different resins can have different barrier properties, and by choosing the appropriate resin, it is possible to enhance the barrier properties of a material. For example, some resins have good oxygen barrier properties, making them suitable for packaging applications where it is important to prevent the infiltration of oxygen.
Adding reinforcing materials or using certain resins can also increase the puncture resistance of a material. Puncture resistance refers to a material's ability to withstand being pierced or penetrated by a sharp object without breaking or tearing. This property is important in applications where the material will be subjected to mechanical stresses, such as in packing or transportation.
Extrusion and adhesive lamination